COMPOSITE TEXTILES

This paper explores the structure, composition, and applications of composite textiles, focusing on the integration of fibers and matrices to produce high-performance materials used in industries such as aerospace, automotive, and construction.”
INTRODUCTION
Composites can provide combinations of properties that no single material will provide for advance applications. Composites can be defined as a combination of dissimilar materials to perform a task that neither of constituent material can perform alone. Therefore composites have varied and wide applications.
Generally a composite is made of components:
- Reinforcement material (textile preforms)- generally physical
Properties of TSC are determined by fibre.
- Matrix (binder) – The function of matrix is to bind the fibrous material together and protect them from outside effect.
There are several forms of synthetic composites such as metal-metal, metal-ceramic, and metal-polymer, ceramic-polymer, ceramic-ceramic, and polymer-polymer combinations.
A composite textile is made of a textile reinforcement structure and a matrix material. Textile reinforcement structure can be made of fibre, yarns or fabrics (woven, braided, knit, nonwovens) and are generally flexible. These structures are called textile performs and can be in various shapes and forms.
Matrix materials can be thermoplastic or thermoset polymers, ceramic or metal. The consolidation of the textile structure with the matrix material produces textile structural composites.
What is Composite?
Composite materials (or composites for short) are engineered materials made from two or more constituent materials with significantly different physical or chemical properties and which remain separate and distinct on a macroscopic level within the finished structure. Typically, composites consist of a matrix material and are reinforcing material. The matrix and reinforcing materials may be metals, ceramics or polymers.

Composites properties:
- High specific modulus
- High specific strength
- Resistant to chemicals and organic solvents
- Excellent fatigue resistance
- Thermal insulted and thermal resistant
- Impact and stress resistant
- Better dimensional stability and conformability
- Low flammability
- Non-sensitive to harmful radiations.
- Non-corroding in salt environments.
Classification of composite textile
The classification of textile composite is given below:
Rigid composite
- Main characteristics are high stiffness, high strength and low density.
- Other characteristics include high temperature resistance, corrosion resistances
Hardness and conductivity depending on the product design for a specific application.
Flexible composite
- Flexible composites are mostly rubber reinforced.
- Natural or synthetic rubbers are used as matrix materials.
- Flexible composites are coated fabrics ,automobile tires ,conveyor belts.etc
Composite Textile Material:
Reinforcement Materials:
For continuous fibre composites, fibre material has a great effect on composite properties. High modulus fibres and yams which have very low extensions under high stresses are used for composites.
The most commonly used fibres are Fibreglass, carbon, and kevlar. Some special includes boron, ceramic, metallic, quartz, silicon carbon and ultra high modulus polyethylene fibre. In recent years benefit and opportunities, offered by natural fibres as composites have been recognized.
Glass Fibre
Glass is extensively used in modern composites, have high tensile strength, but very brittle and extremely sensitive to cracks and defects. When used in composite plastic matrix protects its surface and prevents crack formation, which produces a strong composite. Glass is also used for its low cost. It comes in different types eg. A, C, D, E, E Glass gives special electrical properties, dimensional stability, moisture resistance and low cost. S-Glass has higher tensile strength, high elastic modulus and better thermal stability but also expensive. It is used in advance composites. C-glass is gives chemical resistance. D- Glass is improved form of E- glass.
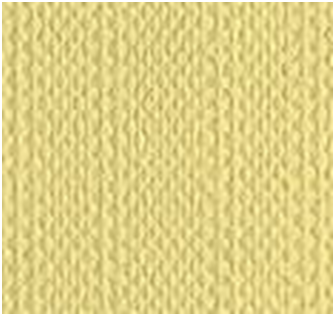
Carbon fibre-
Carbon fibre is produced by heat treatment of organic precursors such as rayon, polyacrylonitrile and pitch. Carbon fibres have highest modulus and strength both at room and high temperature. Carbon fibres are electrically conductive, having low density. Carbon fibres are impregnated with epoxy size to reduce fibre abrasion, fibre matrix compatibility, and to improve handle.
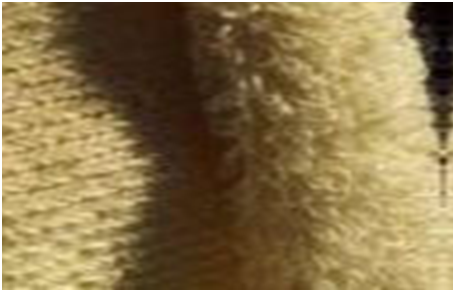
Kevlar Fibre:-
Kevlar is the registered trademark for a light, strong Para-aramid synthetic Fibre, related to other aramid such as Nomex and Technora. They are usually yellow in appearance, low density, High strength, Good impact resistance, Good abrasion resistance, Good chemical resistance, Good resistance to thermal degradation, Compressive strength. It is usually used in bulletproof vests, in extreme sports equipment, and for composite aircraft construction. It is also used as a replacement for steel cords in car tires, in fire suits and as an asbestos replacement.
Matrix Materials
Matrices bind fibrous material together and hold them in particular positions and orientations giving the composite structural integrity. They protect the fibre from environmental effect and handling. It transports the forces and stresses acting on boundary of composites to the fibre and give strength to composite structure. The chemical properties are generally determined by this plastic component.
The reinforcement material and resin must be compatible for good penetration and bonding. Both thermoset and thermoplastic resins are used as matrices in TSC.
Thermoset Resins-
The most widely used thermoset resins include polyester and epoxy. Manufacturers typically use polyester in applications where temperatures remain low. Polyester resins offer several advantages: low cost, low viscosity for good flow and effective fiber surface wetting, and low curing temperatures. However, they also come with drawbacks such as poor strength, weak impact performance, and high shrinkage during the curing process.
Epoxy resins perform well in high-temperature applications and offer a versatile range of physical properties, mechanical performance, and processing options. Depending on the manufacturing conditions, epoxy resins can provide toughness, chemical and solvent resistance, flexibility, high strength, hardness, creep and fatigue resistance, good fiber adhesion, heat resistance, and excellent electrical properties. Examples of commercially available epoxy resins include Tactic from Dow Chemicals, Araldite from Ciba-Geigy, and Epon HPT from Shell Chemicals. To cure epoxy resins, you must use a curing agent.
Thermoplastic Resins
Thermoplastic materials fall into two categories: commodity thermoplastics and engineering thermoplastics. Commodity thermoplastics—such as polyethylene, polypropylene, polyvinyl chloride, and polystyrene—do not resist high temperatures effectively.
In contrast, high-temperature thermoplastics offer greater heat resistance than epoxy. These materials provide improved toughness and superior resistance to heat and moisture. Examples include PEEK (polyetheretherketone), PPS (polyphenylene sulfide), and PEI (polyetherimide).
Table No.1 Properties of Fibres
Fibre | Density(g/cm3) | Melting point *(C0) | Tenacity (g/den) | Stiffness (N/m) |
Glass | 2.5-2.7 | 700 | 6.3-11.7 | 310-380 |
Carbon | 1.79-1.86 | 3500d | 9.8-19.1 | 350-1500 |
Kevlar | 1.38-1.45 | 427-482d | 5.3-22 | 500-1000 |
Steel | 7.90 | 1500 | 2-5-3.2 | 167-213 |
Manufacture of textile preforms
The most common constituent material forms used in textile composites are fibres, fabrics & nonwoven.
Fibre Forms
Short or chopped fibre reinforcement composites are not as strong as the composite structure that allows controlled filament orientation. Continuous fibre reinforced structure with highly aligned fibre arrangement results in high quality and stronger composites. Filament winding is used to produce such structures. In filament winding, continuous filament, fabrics, roving or tapes are wound on a rotating mandrel.
Fabrics
Woven
It can be grouped as two dimensional and three-dimensional structures. In 2-D thickness of the fabric is small compared to its in plain dimensions. Plain, baskets, twill and satin weaves are used, 2-D fabric shows generally anisotropic, have poor in plane shear resistance, and have less modulus than fibre. To increase isotropy, in plane shear rigidity and other properties in bias or diagonal direction, tri-axially woven fabrics are developed.

Braided
It is a major manufacturing process for textile composite performs. It is done by intertwining yarns using an over and under sequence. It shows advantages like versatility, good mechanical properties; surface can be made of different cross sections like cones and nozzles giving near-net shape and low manufacturing cost.
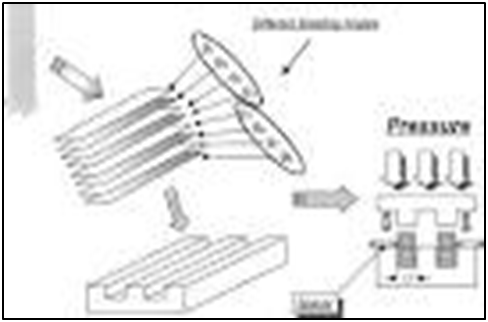
Non woven
Non-woven unidirectional fabrics are used as reinforcing structures in composites. But due to firmness of the binding material, they do not readily conform to complex shapes. They are not as strong as fabric structures. Needle punching and stitch bonding are the methods use to manufacture the nonwovens.
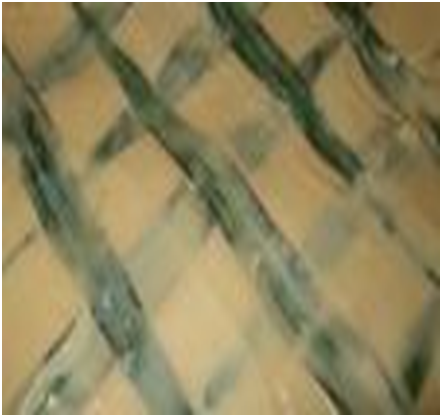
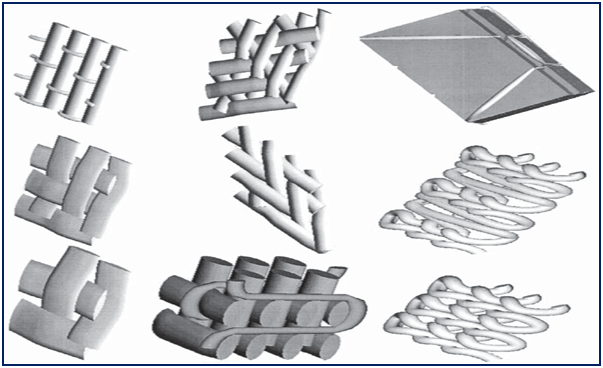
Textile structures: (a–c) 2D woven fabrics; (d) 3D woven fabrics; (e, f) 2D braided fabrics; (g, h) weft-knitted fabrics (i) multiaxial multiply warp-knitted fabric. Woodhead Publishing Limited, 2005 1.1 Textile structures: (a–c) 2D woven fabrics; (d) 3D woven fabrics; (e, f) 2D braided fabrics
Composite Manufacturing
Two major steps in manufacturing of composites are wetting of textile reinforcement structure with resin (matrix material) and curing which is three dimensional formation of a polymer network. During curing, hardening of the resin takes place and bonding is formed between the resin and fibres in the reinforcement structure. Curing can be done unaided or with application of heat and / or pressure for faster polymerization.
Different methods are listed below –
- Prepregging & wet-layup
- Resin Transfer Moulding
- Compression Moulding Processes
- Injection Moulding
- Autoclave & Pultrusion
PREPREGGING
Prepregging involves the application of formulated resin products, in solution or molten form, with reinforcement of carbon, fibre glass or aramid fibre or cloth. The reinforcement is saturated by dipping through the liquid resin. In an alternate method called a Hot Melt Process the resin is impregnated through heat and pressure. The Hot Melt System uses resins with a very low percentage of solvents.
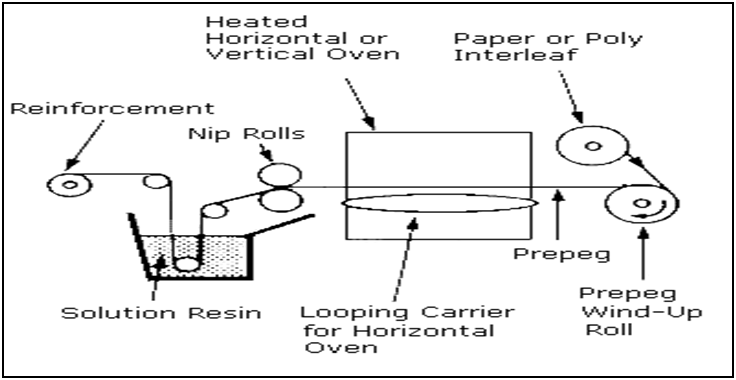
Resin Transfer Molding –
Resin transfer molding is used when parts with two smooth surfaces are required or when a low pressure molding process is advantageous. Fibre reinforcement fabric or mat is laid by hand into a mold and resin mixture is poured or injected into the mold cavity. The part is then cured under heat and pressure.
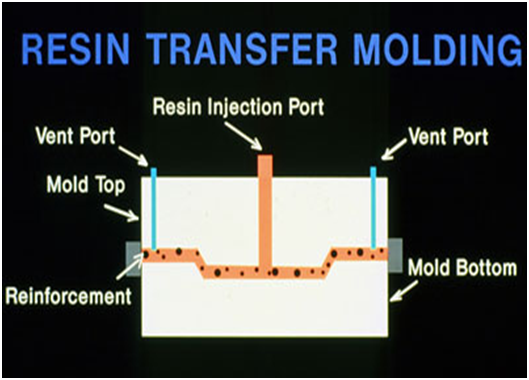
.
Pultrusion –
In the pultrusion process, continuous roving strands are pulled from a creel through a strand tensioning device into a resin bath. The coated strands are then passed through a heated die where curing occurs. The continuous cured part, usually a rod or similar shape, is then cut to the desired length.
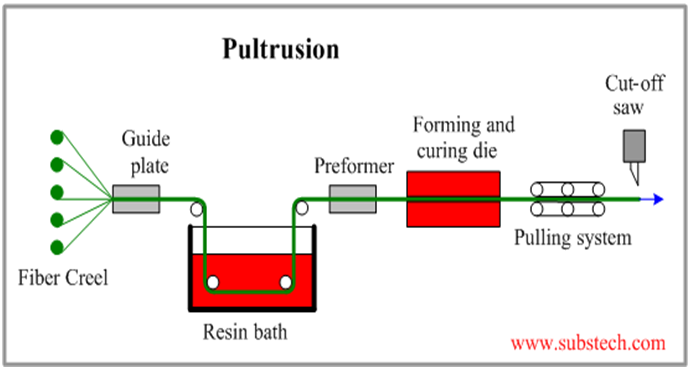
The advantages of textile composites can be:
- Low energy cost during manufacturing
- Long term energy saving due to lighter parts
- Due to anisotropic design, directional properties could be obtained.
- Good fatigue resistance
- High degree of damage tolerance
- Corrosion resistance
- Can be design with varying degree of electrical and thermal conductivity
- Wide range of availability of fibres, yarns, matrix material and manufacturing processes
APPLICATIONS
Area of Application | Features | |
Aerospace | Carbon fibre reinforced composites are mostly used in Aircraft, Rotorcraft, and Spacecraft/Missiles Engines/Nacelle. Airbus. | |
In external application of Aerospace | Glass fiber composite is used in Nose radome, engine pylon parts, and portions of the wings. | |
In sports :-Graphite boron Kevlar epoxy composite | Sport, hockey sticks, Golf carts, hockey sticks, playground equipment, sail boats, helmets, bicycle frames, tennis rackets, arrows. | |
Interior parts | Interior parts are usually made up of Fibre reinforced epoxy. in floors galleys, portions, cargo liners etc. | |
Automotive application | Drive Shafts, side rails, doors, cross members, oil pans, wheels, trunks, and deck. | |
Apparel/Clothing | Aramid fiber and fabrics for reinforcing polymer matrix composites are used in apparel. Due to Thermal Bond ,Thermal Insulation, Flame Retardant | |
Home Furnishing | Textile composites are also used in clothes/ shoes/ beds/wall papers, Blankets etc |
CONCLUSION
The emphasis on composite has increased. The material is having intrinsic sensing, controlling, and actuating capabilities. Composite textiles are now integrated with fibre optic sensors, which will monitor-
The internal stress distribution during manufacturing process
The health and damage of composite textile during services and control the system to react the changed working environment.
The composites can quantitatively determine number of physical parameters, such as, temperature, stress/ strain, thermal expansion, pressure, etc.
Composite textiles are really going to have a dominating and influencing effect on the globalized world and only one phrase suitable to this is “The difference between ordinary and extra – ordinary is a little extra and that extra can be added by means of textile composites only”